Job costing is usually a method of costing apply in industries, where the cost of the production usually measure by the number of completed jobs. This usually takes as a factor to measure the feasibility of jobs.
These costs recorded on a ledger throughout the whole job process and are added to the final balance statement when preparing for job costs and the batch statement.
The job costing method or system can virtually use in any industry and use to check whether if the cost of production exceeds the overheads and the price of the materials, to provide profit for the whole process.
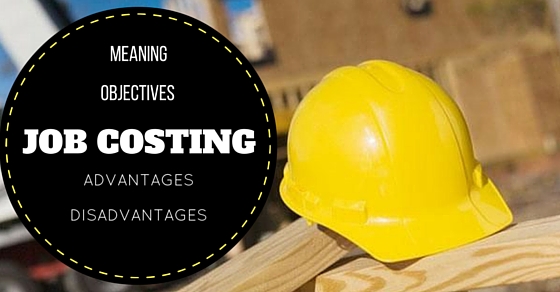
What is Job Costing?
Job costing is a technique of costing where the amount of work done is in the form of the number of jobs completed.
The production takes for the customer’s orders and not as bulk for stocking purposes.
Moreover, the cost does not take singularly but as a bulk of objects.
For example:
Printing 5000 books, assembling 500 cars, delivering 4000 pamphlets and so on.
The elements within the job costing procedure consist of direct costs, employment costs and material costs which comprise of prime costs and also overhead charges used for the departmental costs and shipping and handling costs which also includes costs taken for stocking and storage.
Documents Used in a Job Costing System:
1. Production order:
Production order or cost order is a type of work order, authorizing and sanctioning the manufacturers to produce, the order gives to the customer. This process initiates the manufacturing process
2. Cost sheet:
For recording purposes, another type of document is presently called the cost sheet. The cost sheet and the works order both can be combined at the last stage while establishing the final production value.
3. Other documents:
The other documents are processed and submitted in between the manufacturing processes such as materials order, tool tickets, storage and stocking documents, warehousing, and inspection tickets.
Job Cost Accounting Procedure:
The cost of the direct materials is taken calculated by the help of the materials requisition form. This is tallied by the accounts department. The employee wages are also calculated by taking the tickets issued by the payroll department. Moreover, if any overhead charges, these are also taken under consideration.
Manufacturing overheads are applied, at their respective departments during manufacturing. Then these are calculated together which constitutes the four main expenses of manufacturing. That is direct expenses, direct labor, material expenses and manufacturing overheads within each department.
The job cost accounting procedures as a summary are given below:
1. Receiving an inquiry:
Before placing the order, the customer usually studies the manufacturer, what their rates are, what is the quality of the materials that they use, the time usually takes by them to complete the order and so on.
2. Estimation of the price of the job:
The cost of the job is done by the accountant keeping in mind the needs and taste of the customer. This includes the customer’s preferences and choices. Another factor is that they also keep track of the change in the cost of the materials, especially in recent years and specify the difference in cost. This job cost then sends to future customers.
3. Receiving of order:
The customer will place the order if he is content with the job costs.
4. Production order:
If the job accepted, then a production order gives by the manufacturer within its subsidiaries. It is a form of authorized order which officially starts the production of the job.
It’s a set of instructions directed towards the foreman directing when and how the job should do and how much should be completed in a day. Enough copies made and passed throughout the departments so that each department can parallel keep track of the jobs done.
5. Recording of costs:
The costs record and collected for each kind of job. For each department a certain job card use, where the costs from different aspects of the jobs take into consideration.
These include:
Materials:
1. Material requisition:
Any document issued by the company stating the manufactures to transport the materials from the storage unit to the production house, to start manufacturing.
2. Bill of materials:
A list detailing the materials, prices, components, sub-components for manufacturing the end product.
3. Materials issue analysis sheet:
A form of document which consists of materials, their related details and when it issued for the manufacturers.
Wages:
1. Operation schedule:
It’s a form of the timetable which relates to the allocation and reissuing of resources in an organization.
2. Job card:
A form of the card used to detail the details of the job need to do in a production facility. It instructs the foreman what to do as a set of instructions. Helpful for both the parties involved in the business.
3. Wages analysis sheet:
It is a derivative of the income statement. It consists of the payroll statements and the wages for both the manufacturing and non-manufacturing employees depending on whether if it is a fixed salary or an hourly wage.
Overheads:
Miscellaneous costs:
These include hidden costs such as transportation, stocking, storage, food, infrastructure, etc.
6. Completion of the job:
On the completion of the job, a report stating the completion of the job gives to the accounts department where the final cost calculation takes place. The final cost statement then compares with the estimation cost, to ensure whether it was a profit or loss.
7. Calculating the profit or loss:
These costs calculated when the final expenditure compare with the estimating expenditure.
Objectives of Job Costing:
- To maintain the development of each job, by providing a separate account for each process of the job, to estimate the costs, when transitioning from one process to the other.
- It helps the management in estimating the price of a certain work based on the price of the previous jobs.
- To identify profitable and non-profitable jobs and help and prevent profitless jobs from taking place.
- To differentiate departments from one another based on the cost taken and the number of materials required.
- Provide detailed information on what is happening in each department to the customer and move forward with the plan for the idea of the customer. Any sudden changes in the plan can accommodate, if congruent with the final cost estimation.
- Job costing should be flexible and scalable enough to accommodate any kinds of industrial or commercial jobs available for cost estimation.
Features of Job Costing:
According to Eric Kohler, “Job costing a method of cost accounting whereby cost compile for a specific quantity of product, equipment, repair or other services that move through the production process as a continuously identifiable unit, applicable material, labor, direct expenses and usually a calculating portion of the overhead charge to job order.”
Some of the characteristics of the job costing process are.
- Most of the manufacturing and non-manufacturing entities have acquired the job costing process
- The entities which have adopted job costing manufacture goods over customers demand and not for stocks
- In such entities, the total work assesses into various jobs and also each job appraises as a separate cost unit.
- In this method, the production is not a continuous one
- An account open for particular jobs including all the extra things, to know the exact cost of the job.
- As every job is different, the procedure of job costing for it also differs
- The job of the cost finalizes after the job completed.
- The real-time profit or loss decided, only after comparing the actual cost with the charged cost of the job
- Using job costing, the profit and each job’s cost can found out separately
Here the organization does not have to spend on selling and distribution, the customers are responsible for placing orders and collecting the goods
Some of the Organization types which adopted job costing are:
- Printers Machine tool manufacturing industries
- Interior decorations
- Advertising concerns
- Furniture making industry
- The musical instruments manufacturing industry
- Management consulting industry
- Toy making industry
- Engineering workshop
The above mentioned are few objectives of costing. Now let us look at the advantages and disadvantages of cost accounting
Advantages of Job Costing:
- Job costing acts as a form of analysis detailing all the types of costs that are present throughout the manufacturing process. This includes the direct costs, the labor costs, and the overhead charges.
- It acts as a gauge determining the profitability of the job and helps for future customers or companies to decide whether to take up the job or not. It also gives us an idea about the feasibility of the job.
- Job costing prevents duplication of work because it helps in the estimation of a similar job. This helps in a company quoting the price of a job, it can always depend on the pricing of a previous job as a reference.
- The efficiency of the manufacturers can also take into observation while taking account of their job costing and their associated expenses.
- Ruination and defective work can found out through job costings and it can immediately correct through certain individuals responsible for the job.
- Budgetary control comes into action when taking into consideration the various overhead charges which predetermine for each department.
- Job costing information uses more for job contacts where the price of the job depends on the amount of the work is doing, rather than depending on the final price.
- It evaluates the quality of the work through various statistical techniques.
- Job costing provides an easy calculation of cost overheads for specific needs, and in a precise manner.
- Job costing enables the supervisors to keep track of various components such as money, materials and the performance of the employees.
Disadvantages of Job Order Costing:
- Based purely on costs. This method, disadvantageous in fixing prices for the complete process, as the costs record along each step. Hence it makes it difficult to prevent unwanted costs and expenditures occurred in between the processes.
- It’s very expensive because records are to prepare for every step of the order. Starting from the materials list to the final product statement. Hence capital needs to keep such records properly.
- There no exact procedure for estimating the job cost since there are no specific methods to differentiate direct and indirect costs occurring in a process.
- This method of price estimation, may not be useful for jobs that are cost-efficient and fast-paced.
- No standard procedure to follow while estimating. The only thing that can be followed is the need for supervision when calculating costs. To prevent any miscalculations and forgery of the prices and materials respectively.
- More and more clerical work required to detail the measures and quota takes in every step of the project from the start to the finish.
- Highly expensive because of the number of people working for a single project and unwanted expenditures may also present.
- No control of costs, since quality control and price control usually do after the estimation of the final price. That too price control can also do under a limit. Only to visible price variations, there is a chance of hidden costs that may not be recorded.
- These kinds of jobs are only applicable, depending on the nature of the market and not on the nature of the job assigned. This becomes useless when the behavior of the consumer market doesn’t support such jobs, more and more expenditure for man, machine and materials takes place.
- During inflation and recession, such jobs are useless and comparing such job costs is fruitless and a waste of time. Ordering job costs during the time of inflation not consider smart.
- No form of correction can take place if the actual profit is less than the estimated profit. The only thing we can do while calculating job costs are preventing loss to both the consumer and the manufacturer.
- Since overheads are allocated to each department on a predetermined basis, there is no strict method to control the cost of the project using job costing.
- Record keeping is what keeps the process of job costing alive. If there is no sufficient record work, then it can cause a huge downfall to the whole project and it may lead to a huge loss to the manufacturer.
- There no 100% accurate estimation of the total final cost of a job using job costing.
Job costing is an efficient method in keeping track of the expenditure against the given revenue, that is, the income or the fixed budget by the customer. It expands to all industrial professions and people of different designations.
Job costing depends on the type of work that is doing, rather than applying to any kind of job. This way the result suited to the customer’s needs and choices.
Usually, job costings happen by contractors, architects, and consultants. People who own a small convenience or a hardware store doesn’t have to use job costing techniques. Using job costing helps you to focus on the strongest and the weakest link of the business.
Hence, it helps the manufacturers to focus on the strongest link to produce more and more profits while giving expert care to the weakest links, so as not to provide any unwanted losses.